The best dri sludge distributors on the market
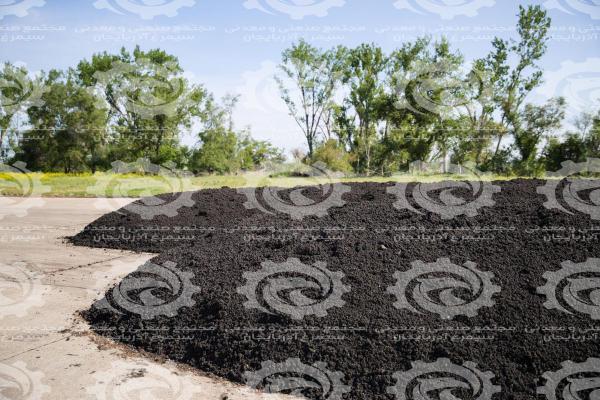
Accordingly, at first, the dry sludge used was analyzed by XRD and XRF methods in terms of available crystal phases and chemical composition, respectively. The results of these analyzes indicated the presence of more than 50% silica (SiO2) in the crystalline phase of quartz in the sludge. Also, the presence of more than 20% organic matter in this material reinforced the idea that these materials reduce the quality of concrete. Therefore, the heating process up to 650 ° C was designed for the initial dry sludge. The results of XRD analysis of the cooked sludge showed changes in the crystalline phases. Due to the occurrence of crystalline changes in this material, there was a possibility of pozzolanic activity (reactivity in cement medium) which was performed to detect STA analysis. For more information about The best dri sludge distributors on the market, visit our site.
Experimental analysis on the use of dri sludge
The results of this analysis indicated that the pozzolanic activity of the baked sludge was inactive. To investigate the effect of dry sludge on concrete properties, two mixing schemes based on water to cement ratio of 0.45 and 0.55 were considered and values of zero, 5, 10, 20 and 30% of dry sludge were used. To investigate the effect of sludge on concrete performance, compressive strength test was considered as a characteristic of durability and treated specimens (three replications) were examined for 3, 7, 28 and 90 days. The results showed that 90-day concrete samples containing 5% sludge, about 4% reduction, samples containing 10% sludge, about 8% reduction and samples containing 20% sludge reduced the compressive strength by about 22% compared to the control sample (without sludge). ) Will have. Since the volume of concrete consumption in the country is very high and due to the very low reduction of compressive strength due to the addition of small amounts of sludge, the authors of this article, while considering the need to study other effects of adding sludge to concrete, use sewage sludge as stone Recommended in amounts less than 10% in conventional concretes such as floor concrete.
These pits can do the job of drying sludge beds and even part of the sludge digestion process together. The height of the sludge in these pits can be selected between one to 3 meters, but it should be noted that the sludge was introduced in 20 cm layers in the pit and after drying, the next layer was added. In this way, it is possible to empty the dried sludge from the pit at intervals of every few years. To calculate the required surface in these pits, the surface load entering these pits is selected to be close to one cubic meter of sludge per meter of the pit surface per year.
Natural pits in the area can be used to create lakes or dry sludge ditches, or with the help of embankments and short empty dams, the desired pits can be created. Sometimes such lakes or natural pits can be used to dry and permanently store sludge and do not plan to empty the dried sludge. In this case, the filling time of the lake is usually considered to be 10 to 15 years. For this method, in order to dry or store the sludge, it is necessary that the groundwater level is low and the permeability of the ground allows natural drainage. Such pits should be away from people’s environment and the direction of the wind and the possibility of creating mosquitoes and unpleasant odors should be predicted. For more information about sheet metal material, visit our site.
Distributing dri sludge at rational price
Drying sludge with heat requires thermal energy and fuel consumption, and is usually expensive and uneconomical unless the gases obtained from the anaerobic digestion reservoir are used to generate heat as an exotherm. For more information about stainless steel sheet metal, visit our site.
You can contact us to buy and sell this product:
Sales consultant: Ms. Leila Nematzadeh
Ways of communication: Phone number: 02147623014
Phone number: 04133660491
Phone number: 09120169267
WhatsApp Response (Skype): click
Instagram: simurgh_steel_company@
email: info@simurghsteelco.com
email: ironore110@gmail.com
Facebook: ironore110@
LinkedIn: simurgh-iron-and-steel-company-a68295180@
twitter: CoSimurgh@