Iron pellets Price Fluctuation
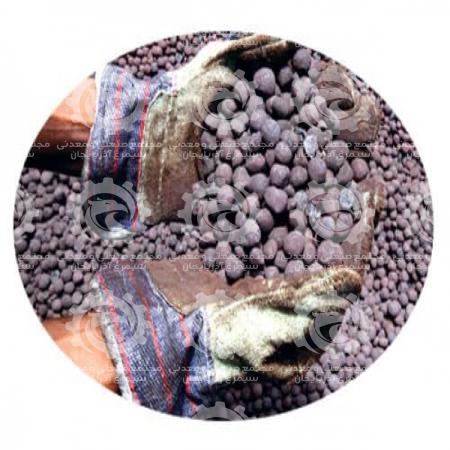
Granulated iron ore is made dry and without water. Then, by means of a physical separation (magnetic method), the high-grade iron ore is separated from its alloys. Granulating iron is not used in the direct reduction system due to its low content, but it can be used in blast furnaces. In concentrators, the average grade of iron ore is low and the amount of elements is more than acceptable. For more information iron pellets visit our site.
How to make iron pellets?
The processing path includes crushing, grinding, upgrading and dewatering units. In addition to these units, there are transportation, water supply, facilities, etc. as auxiliary units. Each of these steps is described separately below. Crushing stage (first stage): In the factory, the crushing stage begins with the entry of the mineral into the crusher. In this part, pieces between 20-25 and 100 cm are broken to sizes less than 25-20 cm. At the entrance to the crusher, a fixed grizzly sieve is installed, the holes of which are equal to the size of the product coming out of the crusher. In this way, the smaller sizes do not enter the crusher and prevent them from getting smaller.
The crushed minerals are then transported to the next step of crushing and screening using a conveyor. It is in this part that depending on the size and characteristics of the minerals, it can consist of 2 dry crushing stages, here a cone crusher is used and the size of the minerals is reduced to 30mm. In order to control the particle size and to avoid excessive grinding of the mineral, grinding is carried out in several stages. Grinding stage (second stage): Minerals smaller than 30mm enter the grinding stage due to additional grinding, which is carried out in a “wet” form. Here, the material is crushed and ground to a size of 0.5-0mm using a self-breaking or semi-self-breaking crusher or pressure roller. Materials with a size of 0.5 to 0 then move on to the next stage where they are pre-crushed and broken using better ball mills.
The grinding of these parts is done in a “wet” environment, the size of the grinding is controlled by hydrocyclones, and the materials which float in the water and have obtained a slurry composition are guided using guide pumps. Upgrade step (third step): At this point, the particles, after reaching the desired fine size in the grinding step, should enter the next step to separate the valuable materials from the intra-slurry waste compounds. Slab contraction joints should cross at post openings and cross at post openings. Magnetic wet separators are drum separators. Slars pass over these magnetically charged drums. The iron ores are attached to the drum and collected from the drum to the end of the drum with the help of a blade. Other minerals present in the slurry are also removed from the bottom of the equipment.
Magnetic separators have low intensity, medium intensity, high intensity, and high gradient (quantity by number) types which are selected based on the characteristics of the minerals and the processing test performed on the mineral. If elements such as phosphorus and sulfur are present in the concentrate, the flotation method is used to replace the waste from the concentrate. Dehydration stage (fourth stage): In the fourth stage, in which dehydration takes place, the high-grade iron ore also contains amounts of water which must be dehydrated and dried, and its humidity must be 10-9%. Filters are used to separate the resulting concentrated water. After that, the dehydrated concentrate is transferred to the product warehouse and stored there. The waste is also sent to an equipment called a Tickner for dewatering.
In this section, the solids settle and water overflows from the top of the thickener. The deposited solid particles are also sent to the center using the Thickner floor collector arm and to the tailings dam using a pump. A chemical polymer called a flocculant is used to speed up settling, causing the waste particles to stick together and speed up their fall. In general, it can be said that the processing of iron ore is different with regard to the mentioned steps. For example, there are several methods of crushing iron ore which should be selected according to the type and size of iron ore, the correct method and device to record the maximum production efficiency. For more information iron pellets price visit our site.
Price changes of iron pellets
Price changes of iron pellets have been mostly due to currency market fluctuations that have affected the price of this product, so you can visit our site about the price of this product and iron ore pellets market.
You can contact us to buy and sell this product:
Sales consultant: Ms. Leila Nematzadeh
Ways of communication: Phone number: 02147623014
Phone number: 04133660491
Phone number: 09120169267
WhatsApp Response (Skype): click
Instagram: simurgh_steel_company@
email: info@simurghsteelco.com
email: ironore110@gmail.com
Facebook: ironore110@
LinkedIn: simurgh-iron-and-steel-company-a68295180@
twitter: CoSimurgh@