Types of sheet metal fabrication
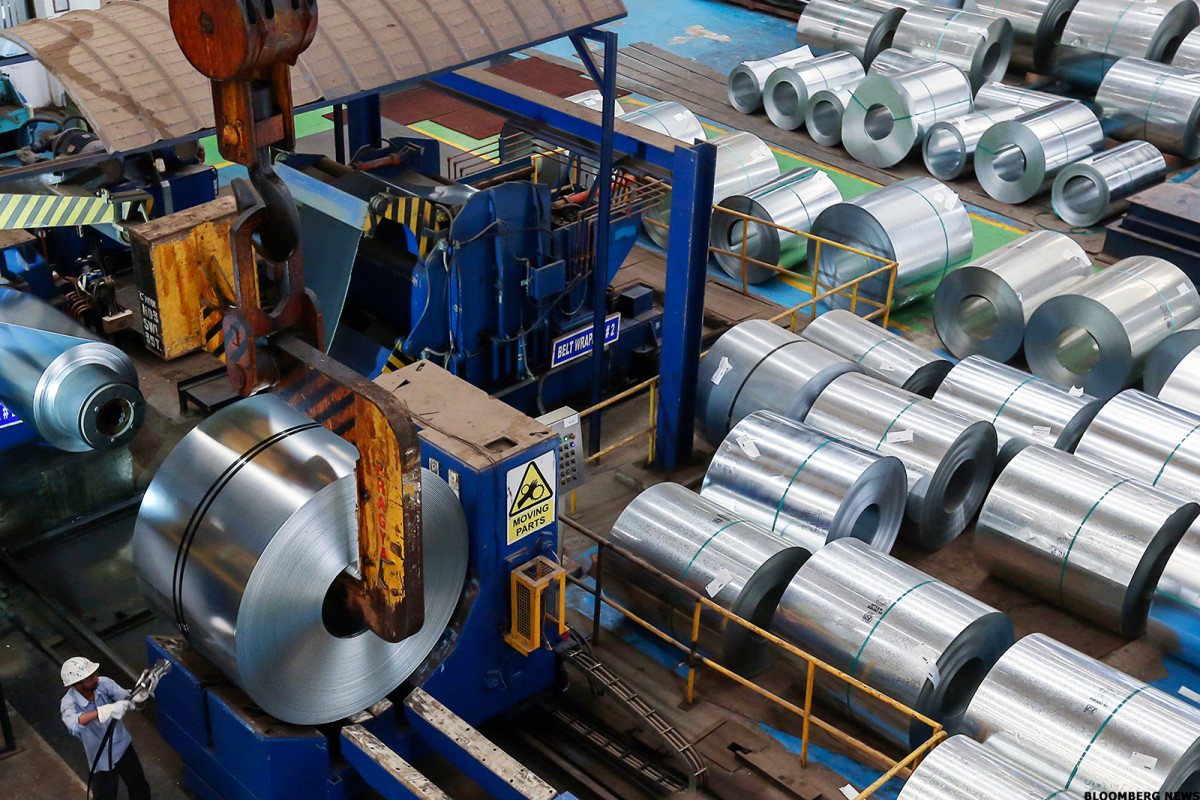
Our culture has a strong affinity for metal steel. Steel is used extensively in the building of a wide variety of things, including but not limited to houses, schools, hospitals, bridges, automobiles, and trucks, to name just a few examples. Solar panels, wind turbines, dams, and electric vehicles will all depend on steel to varying degrees, making it an essential component of the energy transition. Steel will also be a crucial ingredient for the energy revolution. Since 1970, the demand for steel across the globe has surged by more than three times its level, and this trend is expected to continue as economies expand, urbanize, become more consumer-oriented, and invest more in their infrastructure.
The iron and steel industry is ranked first when it comes to the emission of carbon dioxide (CO2) and is ranked second when it comes to the use of energy among heavy industries. The production of iron and steel is directly responsible for 2.6 gigatonnes of carbon dioxide (Gt CO2) each year, which is equivalent to seven percent of the total global emissions from the energy system and more than the emissions produced by all freight transportation by road. 1 At the moment, the steel industry is the greatest industrial consumer of coal, and coal supplies approximately 75 percent of the energy that the steel industry requires. Coke is an essential component for the series of chemical reactions required to produce steel from iron ore, and heat generated from burning coal is utilized for both of these purposes.
Sheet metal fabrication products
The forming and working of sheet metal is one of the production techniques that is most frequently used. The volume to surface area ratio is much smaller in sheet forming than in the mechanical forming procedures discussed above. Uses for big-area sheet products include automotive bodywork, airplane frames, huge home appliance housings, and construction fixtures. However, there are a plethora of uses for smaller sheet metal components, such as washers, beer cans, kitchenware, and cutlery.
Mild steel, aluminum, and stainless steel are the three main types of sheet metal that are commonly offered for sale. The most frequently utilized for auto restoration are the first two. Here is a careful examination of the variations among these three categories of sheet metal and the advantages of each.
- Mild Steel-Fenders, firewalls, and door skins are excellent examples of parts that are well suited for mild steel application. It is simple to weld and unlikely that this kind of sheet metal will rip or tear. Mild steel is the best option if you need light sheet metal.
- Aluminum- Aluminum is perfect for dashboards since it is lightweight and generally simple to handle. It can also be coated and given a colored anodizing, and it does not rust as quickly as steel. Additionally stronger than steel, aluminum is completely recyclable.
- Stainless Steel- An alloy of iron, nickel, chromium and other metals produces stainless steel. It is exceptionally durable since it has a high level of oxidation resistance. Due to its high melting point, stainless steel is perfect for creating and assembling automobile parts including brackets, panels, and tubing as well as interior trim components.
Sheet metal fabrication uk
Henderson Fabrications UK Ltd is an established firm providing manufacturing and precise engineering services to a multitude of sectors. The company seeks to deliver unique solutions to all your sheet metalwork requirements.
Cutting, punching, folding, and assembling flat sheets of steel or aluminum into metal structures or goods is known as sheet metal fabrication. By cutting and burning the metal, sheet metal can be twisted, stretched, or carved into almost any shape. The method of fabricating sheet metal can also make use of specialized tools like chopsaws and bandsaws. These make sure the process is carried out with even cutting. Large sheet metal portions may be easily and quickly cut with cutting torches. Press brakes are used in sheet metal fabrication to make it easier by assisting in the creation of precise bends and angles in the metal. Press brakes come in a wide range of varieties, each with a unique set of uses and functions. Welding is one of the other key elements in sheet metal fabrication. After each component has been produced, it is assembled and tack welded into place. In the manufacturing of sheet metal, a variety of welding procedures can be utilized to avoid warping or any other anomalies. These methods include unique straightening procedures, staggered welding, employing a sturdy fixture, and coating the metal with sand throughout the cooling phase. An oxy-acetylene torch can be used to straighten metal with defects. To eliminate any imperfections, gentle heat is given to the metal. The typical finishing process for metal involves sandblasting, priming, and painting. This then guarantees the metal has a great appearance and is prepared to be delivered to the client.
Sheet metal fabrication applications
Sheet metal is used in a huge variety of applications, including the bodywork of cars and trucks (lorries), large appliances, aeroplane fuselages and wings, tinplate for tin cans, roofing for buildings (architecture), and many other things. Transformers and other electric devices use laminated steel cores, sheet metal made of iron, and other materials with high magnetic permeability. In the past, plate armor worn by cavalry was a significant application for sheet metal. Today, sheet metal is still widely used for ornamental purposes, especially in horse equipment. Workers in the sheet metal industry are also referred to as “tin bashers” (or “tin knockers”) because they smash panel seams together when putting up tin roofing.
The building of the great majority of aeroplanes involves the use of sheet metal in some fashion or another. On tube and fabric aeroplanes, aluminum is widely utilized for the construction of cowlings, fairings, and other components. Even if you are not planning to construct an aeroplane out of aluminum, there is a significant possibility that you will make use of the many sheet metal skills available to you during the construction of your aircraft. The vast majority of contractors will prefer that their employees have at least a basic awareness of the procedures for working with sheet metal.
Building an aluminum aeroplane involves five fundamental steps. These include (1) Planning; (2) Basic construction; (3) Assembly, rigging, and system installation; (4) Inspection; (5) Final painting. Prior to their test flight, some builders choose to paint their aircraft, while others choose to wait until after several hours of flying time to see if any extra rigging is required or if any other issues arise that would necessitate some disassembly. The majority of sheet metal work also involves several fundamental activities. These include drilling, countersinking or dimpling, bending, cutting, and riveting.
Sheet metal manufacturing process pdf
When an engineering process occurs, the necessity for sheet metal fabrication develops. Sheet metal is created in compliance with the engineering specifications. The manufacturing of sheet metal involves a number of different operations, including shearing, bending, notching, shrinking, and beading. Tools for sheet metal fabrication are used particularly to mold sheet metal into parts and components.
Understanding the Processes Involved in the Fabrication of Sheet Metal
The steps taken in sheet metal fabrication are described in the following details:
- Utilizing blueprints
The sheet metal product requirements will be specified in accordance with the engineer’s drawings. To comprehend the breadth of the fabrication process, rough sketches will be developed.
- Complete the drawings
The final shop drawing will be created once all the specifics have been resolved. Here, intricate calculations are performed to ascertain the degrees of stress on the various sheet metal components. The process to be followed in terms of fabrication will be decided by this study and computation.
- Metal Manufacturing
This is the actual process of fabricating metal, in which raw materials go through a number of steps to produce the finished product. This item was made in accordance with the budget and design specifications.
- Finishing of Products
After it has been constructed, the product must go through several finishing procedures to make it marketable.
An excellent product is produced as a result of the many sheet metal manufacturing stages. Each phase contributes to ensuring that the final product complies with the design requirements. The actions listed above should be taken to establish a clear working relationship between the client and the fabricators. Such a procedure will bring about a growth-friendly environment.
Sheet metal fabrication machines
Today, the fabrication of sheet metal is a significant industry. Metal sheets must be cut, welded, molded, and put together.
In the past, physical labor was used, but today we have highly specialized equipment and technologies to lighten the workload and produce better results. To meet the increasing workload of industry attempts, metal fabrication, which is a multi-stage process, requires cutting-edge technology and machine-driven skills.
In large companies, it is practically impossible to complete tonnes of metal cutting, molding, and assembly tasks by hand; as a result, it is vital to introduce machines to facilitate their work. Different sorts of machines are employed to do the task depending on the type of necessity.
Welding is one of the most challenging steps in metal sheet manufacturing because it requires a unique straightening procedure, sand covering while cooling, the use of a sturdy fixture or staggered welding to avoid wrapping or other anomalies.
Using an oxy-acetylene torch, straightening faults can be eliminated by progressively heating the metal to eliminate irregularities.
Sandblasting, priming, and painting complete the process. Sharp breaks are also employed in the manufacturing of sheet metal in order to produce acute bends and angles.
- Lathe Machine
- Grinding Machine
- Drilling Machine
- Broaching Machine
- Shaper Machine
- Saw Machines
- Planer Machine
- Hobbing Machine
- Shearing Machine
- Drill Press
- Hem Band Saw
- Iron Worker
- Press Brake and Cambering Machine
- Cold Saw
- Oxy- Gas Torches
- Magnetic Drill
sheet metal fabrication industry
The global sheet metal market size was valued at USD 262.2 billion in 2019 and is expected to expand at a compound annual growth rate (CAGR) of 5.0% from 2020 to 2025. Sheet metal is one of the common building materials used across the construction sector for various applications. Continuous expansion of the building & construction sector is one of the key drivers for the metal market.
Sheet metal products have high strength and are deployed in sturdy structures. Moreover, these products are thin and lightweight, which makes them easy to transport. They are ideal for use in various weather conditions and provide moisture and corrosion resistance. Other advantages of using sheet metal include durability, recyclability, and widespread availability, thus making it a suitable choice for use in construction applications.
It is anticipated that the increased utilization of lightweight materials and alloys composed of titanium and aluminum would help the expansion of the industry. Titanium is a superior metal over steel in terms of both strength and weight. In order to increase its physical and chemical qualities, it is alloyed with iron, aluminum, manganese, and sometimes even other metals. Because titanium is used so extensively in the aerospace industry, there is a good chance that demand for titanium metal will increase in the coming years. Some of the applications for titanium metal in the aerospace industry include aircraft skin, structural parts, engine components, hydraulic systems, missiles, and rockets.
Steel is quite important in our culture. Steel is widely employed in the construction of buildings, hospitals, schools, bridges, automobiles, and trucks, to name a few. Steel will also play an important role in the energy transformation, as it is employed to varying degrees in electric vehicles, wind turbines, solar panels, and dams. Steel demand has more than tripled since 1970 and has continued to rise as economies expand, urbanize, increase commodity consumption, and create infrastructure.
Our committed team will work hard to deliver any unique steel goods you need. CE-certified steel specialists committed to quality and efficiency.
Contact us today for a free, no-obligation estimate.
You can contact us to buy and sell this product:
Sales consultant: Ms. Leila Nematzadeh
Ways of communication: Phone number: 02147623014
Phone number: 04133660491
Phone number: 09120169267
WhatsApp Response (Skype): click
Instagram: simurgh_steel_company@
email: info@simurghsteelco.com
email: ironore110@gmail.com
Facebook: ironore110@
LinkedIn: simurgh-iron-and-steel-company-a68295180@
twitter: CoSimurgh@