Top notch iron pellet for sale
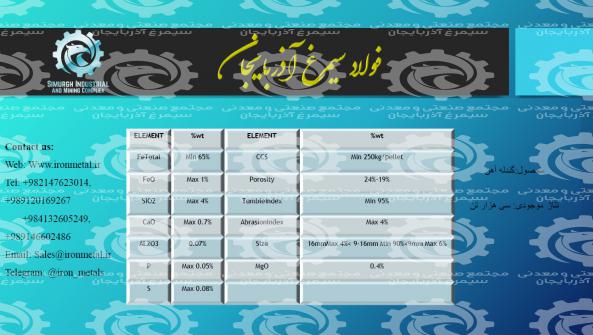
In iron production it was called direct reduction. In this method, the reducing agent and the conversion of iron oxide to metallic iron is natural gas and the direct reduction process occurs in a solid state. In this method, the iron ore is granulated after crushing and enters the reactor. For more information about top notch iron pellets, visit our site.
What is iron pellets used for?
The direct reduction of sponge iron has a short history of 50 years compared to the old and traditional method of iron production by blast furnace. The production of iron through blast furnaces has many advantages that no method has yet been able to replace, and 94% of the world’s iron is still produced from that method, but reasons such as environmental problems and the decrease in coal reserves have led to new methods of iron recovery. Direct reduction or sponge iron production was first done by American and Mexican researchers in the 1970s. Resuscitation is performed in direct resuscitation methods, such as in the abdomen of a blast furnace, and the resuscitation gas acts on the iron oxide and reduces it in several steps.
The iron oxide feed in this method is in the form of porous granules to be able to pass the reducing gas. Reduction gas in direct reduction reactors Before entering the reactor, in the reformers, natural gas (CH4) decomposes and becomes CO and H2, and after preheating to a temperature of 1000 ° C, it enters the reactor of direct reduction. In direct reduction methods, at least 90% of the iron oxide in the granule is converted to metallic iron, which is the ratio of the total iron formed to the total iron in the granule and the percentage of metallization.
The product from the direct reduction reactor, which is in the form of solid sponge iron, is easily loaded directly into electric arc furnaces (EAF) at a temperature of about 600 ° C, where refining and steelmaking is carried out. The sponge iron granules are transferred to an electric arc furnace (EAF) and after removing impurities and reaching the proper composition, they are prepared as primary products such as slabs. Here, scrap is first poured into an electric arc furnace using special baskets, and then a mixture of sponge iron and slag-producing materials such as lime, coke, bentonite, and other additives are added to the melt at the top of the furnace.
At the same time scrap is melted, after sampling, oxygen blowing and homogenization, as well as various analyzes, it is turned into molten steel. Click to familiarize yourself with the different types of arc furnaces. After draining the slag, the molten mixture is sent to the continuous casting unit by means of melt-carrying ladles. In a continuous casting unit, the melt is poured through a nozzle into a container called a tandish and then into a liquid hydrogen copper mold, which is turned into a frozen ingot by spraying cold water along the path of the roll. Finally, the produced slabs are cut to the desired lengths. It is produced from slabs after metallurgical processes of sheet metal and other steel sections. For more information on iron ore pellet specifications please visit our site.
Purchase Top notch iron pellet
iron pellet density is gaseous. In this method, natural gas regenerator is usually considered methane (CH4). Therefore, you can visit our site for more information about Purchase Top notch iron pellet.
You can contact us to buy and sell this product:
Sales consultant: Ms. Leila Nematzadeh
Ways of communication: Phone number: 02147623014
Phone number: 04133660491
Phone number: 09120169267
WhatsApp Response (Skype): click
Instagram: simurgh_steel_company@
email: info@simurghsteelco.com
email: ironore110@gmail.com
Facebook: ironore110@
LinkedIn: simurgh-iron-and-steel-company-a68295180@
twitter: CoSimurgh@