Top notch hot rolled coils Local Suppliers
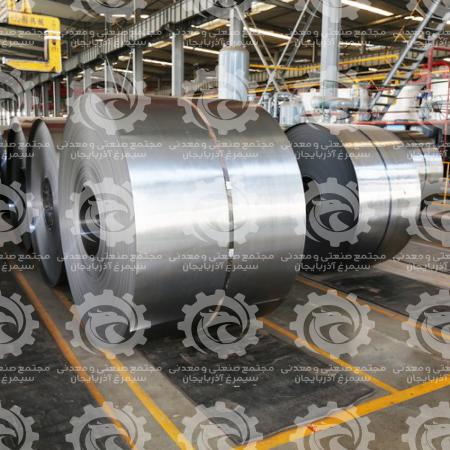
Compared to hot rolled steel, cold rolled steel using stress solidification has a spread of about 20% in terms of quality. It can be obtained by forming cold rolled steel forms, improving separation, estimating semi-finished, semi-rough machining, roughening and finishing Cold rolled steel makes it possible to produce very precise shapes. Visit our site for more information on top notch hot rolled coils Local Suppliers.
The specifications of hot rolled coils
Rolling is the method of forming metal and the raw material for the production of steel products is ingots or slabs. Before entering the rolling process, raw materials or ingots and plates must be produced. Steel ingots are produced and prepared by continuous casting. Continuous casting produces plates that have a rectangular appearance (4.5 to 10 m) long and 20 cm thick. The molten steel is distributed through copper containers and enters the containers at the beginning of the production lines as a freezer that is continuously cooled with water.
When the surface of the molten metal inside the mold reaches a certain height, the ingot and the base of the mold are pulled down by a machine and moved downwards. At this point, the molten ingot enters the secondary cooling area under the mold. It happens. Meanwhile, molten steel is constantly added from above. To prevent the ingots from sticking to the mold wall during casting, a vertical oscillating motion with an oscillation range of 15 to 30 mm is given to the mold. There are also air conditioners that cool frozen metal on the rolling route.
In this area, the ingot is cooled with water so that the freezing process progresses towards the ingot core and after leaving this area it is completely solidified. The secondary cooling area is designed to irrigate the pressure nozzles. Sprayed on all surfaces of the ingot as a powder of about 0.2 to 0.3 MPa and cooled evenly. Water consumption in this area is generally about 0.5 to 0.8 cubic meters per ton of steel. With the end of this stage and the formation of the steel, it is the return of the cutters that can be in the form of scissors or cut with oxyacetylene gas.
Cut blocks that still have the desired temperature can now be directed to the next process. The homogeneity and perfection of the ingots in this method resulted in less production waste and more economical production during rolling. By this method, most non-ferrous metals, carbon steels and alloys can be cast. Since the application of this method, significant advances have been made in application techniques. Hot Word is used to produce different size pages, each with a specific shape and smooth surface. Boards are divided into three categories according to thickness: thin, medium and rough.
Thin layers are considered to have a thickness of less than 3 mm, middle layers between 3 and 75.4 mm, and coarse layers more than 4.75 mm. To produce thin sheets, blocks prepared for rolling or sheets or sheets about 100 to 250 mm thick are first driven into the furnace. The slabs are heated in furnaces to about 1000 to 1250 ° C and melted. The block then enters the front cylinders and after going through these stages its thickness is reduced to 20 mm. It then goes into other rolling stages to produce plates of less thickness and different properties. For more information on hot rolled coil export visit our site.
Local Suppliers of Top notch hot rolled coils
Our company is one of the Local Suppliers of Top notch hot rolled coils and delivers this product to the customer at a good price. Therefore, you can visit our site for more information about hot rolled coil types.
You can contact us to buy and sell this product:
Sales consultant: Ms. Leila Nematzadeh
Ways of communication: Phone number: 02147623014
Phone number: 04133660491
Phone number: 09120169267
WhatsApp Response (Skype): click
Instagram: simurgh_steel_company@
email: info@simurghsteelco.com
email: ironore110@gmail.com
Facebook: ironore110@
LinkedIn: simurgh-iron-and-steel-company-a68295180@
twitter: CoSimurgh@