Sponge iron Wholesale price
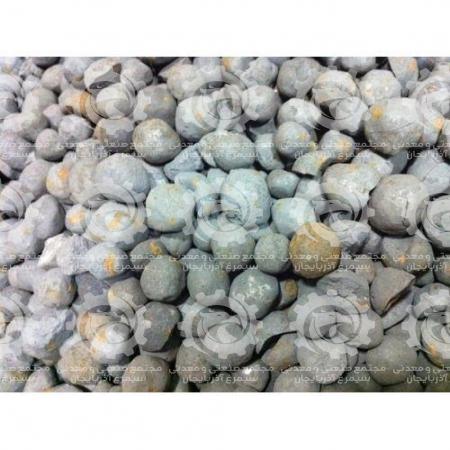
sponge iron is obtained by direct ore and is also called DRI. The use of sponge iron in induction one of its most important applications. It can the use of sponge iron in induction furnaces is able to replace scrap by about 50%. But its application in induction furnaces requires technical knowledge and experience. The use of sponge iron is also a major development in the continuous casting of the steel industry. Many small and large units in the country use these methods. We have more natural resources available for direct regeneration. For more information about Sponge iron Wholesale price, visit our site.
What is sponge iron used for?
The choice of direct iron depends on the location of the manufacturer and the available resources. For example, in Iran, despite the rich gas resources, the choice of gas resources is a more sensible choice and gas is used as a reducing agent. As you know, using coal resources for regeneration also causes air pollution problems and access to its mines is not easy. But currently the largest producer of sponge iron in the world is India, which uses the resources of coal.
From the removal of oxygen in iron ore by reducing gases or carbon derived from city gas and coal, sponge iron is formed.
The term “direct reduction of iron” or direct product of iron is derived from the chemical changes that occur in blast furnaces under the influence of high temperatures.
Iron reduction refers to the process by which iron oxygen is reduced to iron. Production of steel by direct reduction method requires 5 main operations, which include the preparation of concentrate from the mine, conversion into pellets, sponge iron, steel ingots and finally conversion into steel sections such as: beams, rebars, etc., and the resulting rigid product This process is also called “direct iron product“.
Reducing gas is a combination of hydrogen (H2) and carbon monoxide (CO) gases and the furnace temperature in the iron reduction process is about 800 to 1200 ° C.
Iron ore, which is compressed into pellets and is used in the production of sponge iron, contains 65 to 72% of iron and other materials, and the size of each pellet is between 6 and 16 mm. In general, methods of producing sponge iron It is classified into two groups: 1- Gas-based methods 2- Coal-based methods
In both methods, the goal is to separate the oxygen present in different types of iron ores (iron ore, concentrate, oxide shell, pellets, etc.) to convert iron ore to iron metal at a temperature below its melting point. (Less than 1200 degrees Celsius). And it can be said that the production of iron by the process of reducing iron (sponge iron) is almost energy saving. Because it requires less heat and fuel and does not need traditional blast furnaces. DRI (abbreviated as sponge iron) is often converted to steel in electric arc furnaces for maximum heat utilization. For more information about melting point of sponge iron visit our site.
Bulk price of sponge iron in 2020
sponge iron composition In the iron reduction process, the problems of traditional blast furnace methods have almost been overcome. And sponge iron is mined well all over the world. The initial capital and operating costs of iron recovery are much lower than the cost of production in integrated steel mills, and it is also a more suitable method for developing countries with limited coal resources. For more information about Bulk price of sponge iron in 2020, visit our site.
You can contact us to buy and sell this product:
Sales consultant: Ms. Leila Nematzadeh
Ways of communication: Phone number: 02147623014
Phone number: 04133660491
Phone number: 09120169267
WhatsApp Response (Skype): click
Instagram: simurgh_steel_company@
email: info@simurghsteelco.com
email: ironore110@gmail.com
Facebook: ironore110@
LinkedIn: simurgh-iron-and-steel-company-a68295180@
twitter: CoSimurgh@