sponge iron sludge manufacturing process
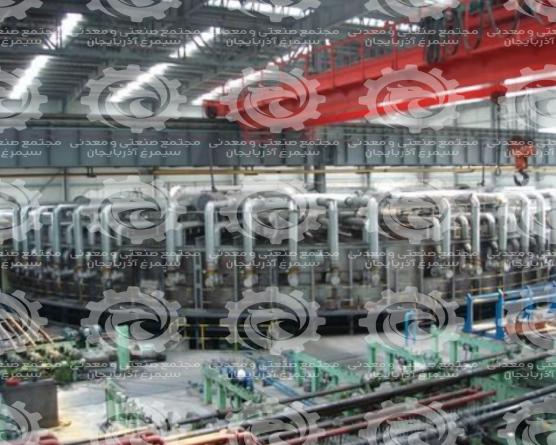
Sponge iron is a product of the direct regeneration of iron ore (pellets). In the immediate recovery operation, without the need for iron ore smelting, its oxygen is removed and its appearance becomes spherical sponge iron sludge, and the reason for naming it is the same spongy appearance of this product.
How to tell the purity of sponge iron sludge
A direct regeneration plant is a unit in which oxide pellets are converted to sponge iron for use in electric arc furnaces. Direct reduction of iron oxide is a chemical reaction in which the reactants are hydrogen, carbon monoxide, and iron oxide, and the result of this reaction is the production of the metal iron. The main fuel of the gas plant is CH4. In general, the direct reduction process has three general steps: reduction, reforming, and heat recovery (Sponge iron making with iron sludge). During the pellet regeneration process, fin (soft) is produced for various reasons such as low pellet strength. Also, most of the soft tissue is formed at the sites of material fall (diverters, feeders, screens, etc.), which are collected by dust collectors as well as with proper cleaning of the environment. One of the main methods of soft collecting is the use of industrial dust collectors, the suction lines of which are used to collect fins in different places, such as diverters and feeders.
Processing steps for sponge iron sludge
The raw material of the direct reduction unit is iron pellets, which during the production process of sponge iron, about 5% of the raw materials are converted to iron, and these wastes are obtained as sludge from gas washing and softening dust from the regenerating unit. Sponge iron molds accumulate, which wastes the company’s capital. The furnaces used in this company are Midrex regenerative furnaces in which the pellets enter from the top of the furnace and after contact with the hot regenerative gases that enter the furnace uniformly through the Bastel line, the pellets are regenerated. The nominal production capacity of each direct steel recovery unit of this company is about 829 thousand tons and the total for two modules is about 1.95 million tons. Due to its low weight, the iron softener is not able to be charged in electric arc furnaces, and due to the problems of carrying softness, it is not very attractive for other industrial owners to buy it. Production of sponge iron powder by reduction, by converting the soft to the briquette, it can be re-entered into the production cycle so that for the following reasons, it can be used in an electric arc furnace:
You can contact us to buy and sell this product:
Sales consultant: Ms. Leila Nematzadeh
Ways of communication: Phone number: 02147623014
Phone number: 04133660491
Phone number: 09120169267
WhatsApp Response (Skype): click
Instagram: simurgh_steel_company@
email: info@simurghsteelco.com
email: ironore110@gmail.com
Facebook: ironore110@
LinkedIn: simurgh-iron-and-steel-company-a68295180@
twitter: CoSimurgh@