Iron pellets export types in bulk
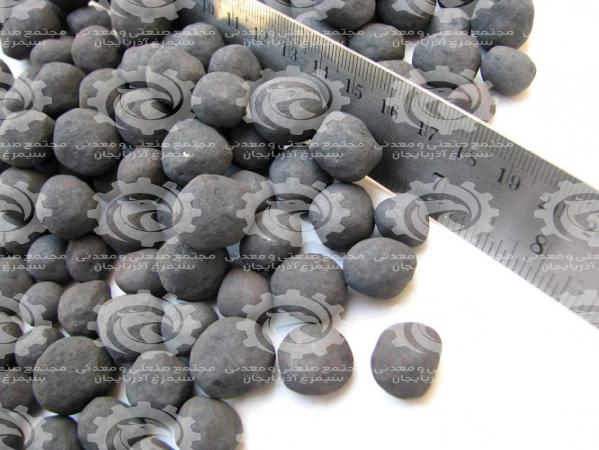
In a DR process, iron ore pellets and / or pellet iron ores are reduced with a reducing gas to produce DRI or hot briquetted iron (HBI). Depending on the production of the reducing gas, two different DR processes are commercially available: gas-based and coal / oil-based. In the gas-based DR process, the reduction gas is produced by chemically reforming a mixture of natural gas and off-gas from the reduction furnace to produce a gas rich in hydrogen and carbon monoxide. For more information on iron pellets export types visit our site.
What are iron pellets?
Typical examples of the coal-based process include the SL / RN and ACCAR processes. Coal-based DR process is more popular in India and China. Different types of reactors such as shaft furnaces, fluidized beds, rotary furnaces and rotary hearth furnaces have been used in different variations of the process to achieve the required metallization. According to statistics (Anon 3, 2014), India is the world leader in DRI production, producing about 17.8 Mt of DRI in 2013, which is about a quarter of DRI production. Gas-based DR processes produce almost 80% of DRI in the world.
is the basic type of gas-based DR processes that accounted for approximately 63.2% of world DRI production in 2013, followed by HYL (15.4%). Therefore, the following discussion focuses mainly on the MIDREX® process. There are two main types of pelletizer used to produce iron ore pellets on an industrial scale: rotary drum and disc. Besides iron ore agglomeration, these pelletizers can also be used for other materials such as copper ore, gold ore, coal and fertilizer [12]. The rotary drum pelletizer was first used for taconite pellets in the early 1940s .
A large drum-shaped cylinder is raised slightly at one end, about 3-4 °. The mixture of iron ore and binder enters the high end and the finished pellets exit at the lower end. To separate the pellets in the desired range from small and large size, a roller screen is usually fitted at the outlet, the last two streams are recirculated (large size after crushing). The recirculation load tends to be about 150-250% of the feed weight. Disc pelleters are also widely used around the world. The advantage of the pelletizer disc is that there is no recirculation.
The desired mixture is fed into the pelletizer, a large disc inclined 40-60 ° to the horizontal. The rotation of the disc leads to the formation of seeds that grow into full-size pellets. Factors affecting the final pellet size include disc angle, feed rate, water addition and rotation speed. As the diameter of the pelletizer increases, the speed should be reduced, otherwise the pellets will start to break due to the high impact. Disc pelleters are very simple to design and has excellent performance For more information on iron pellets types visit our site.
Exporting iron pellets in bulk
Exporting iron pellets in bulk in different packages is done by our company to other countries and customers of many Asian and European countries also buy this product. Therefore, you can visit our site for more information about iron pellets sale.
You can contact us to buy and sell this product:
Sales consultant: Ms. Leila Nematzadeh
Ways of communication: Phone number: 02147623014
Phone number: 04133660491
Phone number: 09120169267
WhatsApp Response (Skype): click
Instagram: simurgh_steel_company@
email: info@simurghsteelco.com
email: ironore110@gmail.com
Facebook: ironore110@
LinkedIn: simurgh-iron-and-steel-company-a68295180@
twitter: CoSimurgh@