Iron ore of india classifications
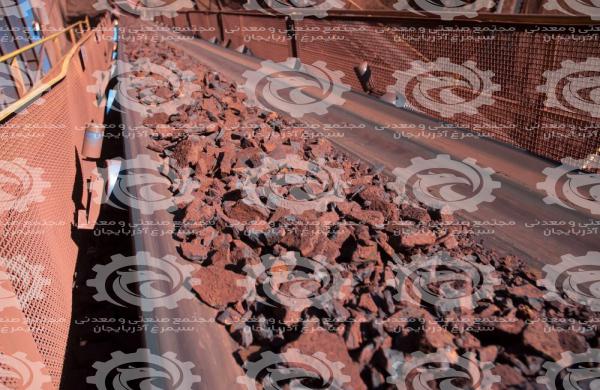
Iron ore is a metal element and covers 5% of the earth’s crust. By extracting raw iron ore from the earth and removing impurities, a dark silver-brown powder of iron is obtained. This element is easily oxidized and is not very strong on its own, and to increase its strength for use in areas such as construction, its alloy is prepared using many iron ore of India. These elements are different and the most common are nickel and chromium.
Who is the largest producer of iron ore?
Sponge iron is a product of direct reduction of iron ore. (Iron ore means pellets) Indirect regeneration operations, oxygen is removed without the need for iron ore smelting. Its appearance is in the form of spherical pieces (porous) porous or sponge-like, which is the reason for naming it, the same spongy appearance of this product. Sponge iron has a high grade of iron. One of the reasons for the spread of sponge iron was the lack of iron waste and the increase in its price and environmental problems. In the following, we will talk about the benefits of sponge iron over scrap.
In English, the direct restoration of iron ore is called Direct Reduced Iron, which stands for DRI. But not all of this iron is present in spongy iron freely, and some of it is in the form of FeO or iron oxide. To measure the amount of free iron in sponge iron, there is an indicator called metallization or ironing. For iron ore uses, if the degree of ironing of sponge iron is 91% and the total iron in sponge iron is 91%, multiplying these two numbers together indicates the amount of iron that is pure and melts in sponge iron. That’s 91 percent. 91 percent = about 83 percent. This means that about 17% of this sponge iron does not contain pure iron.
Different kinds of iron ore of india
Iron is not found in nature in its pure form but in the form of iron oxide, which we know as iron ore. Therefore, for steel and its formation, it is necessary to first separate the oxide from the iron, which is called the process of separating oxygen from iron. The iron obtained in this way is due to the separation of oxygen from it in the form of a cavity and is similar to a sponge, and for this reason, it is called sponge iron. As a result, sponge iron is the product of the process of direct reduction of iron ore. According to studies based on economic, how is iron ore mined, the optimal amount of iron to restore iron oxide is about 67%, which is usually about 90 to 94% of the iron in sponge iron after recovery. This means that iron ore, or pellets or concentrates, reaches about 91% with 67% Fe in the regeneration process, for example by the Midrex method.
You can contact us to buy and sell this product:
Sales consultant: Ms. Leila Nematzadeh
Ways of communication: Phone number: 02147623014
Phone number: 04133660491
Phone number: 09120169267
WhatsApp Response (Skype): click
Instagram: simurgh_steel_company@
email: info@simurghsteelco.com
email: ironore110@gmail.com
Facebook: ironore110@
LinkedIn: simurgh-iron-and-steel-company-a68295180@
twitter: CoSimurgh@