Iron ore for smelting process
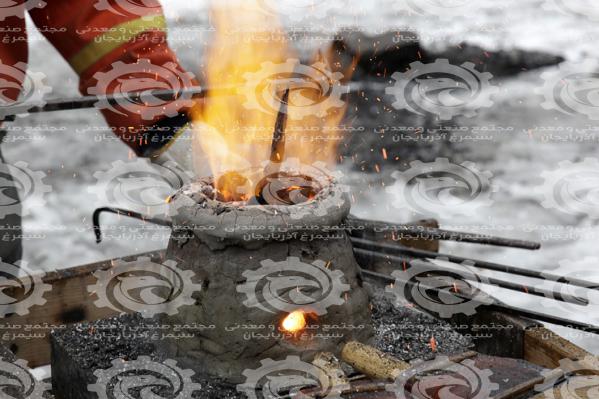
Today, one of the most fundamental economic and social foundations in the world is the iron and steel industries, and this is due to the urgent need that human beings have to advance their goals in life. A brief look at the effectiveness of this vital element reveals its constructive role; Because in addition to its use in construction, bridge construction, iron ore for smelting. it is one of the basic goods in the automotive, shipbuilding and locomotive industries, and as various alloys, it forms the basis of machine technology.
Specifications of iron ore for smelting
The process of extracting iron from natural iron compounds evolved over time until the first iron ore furnace was modernized in the style known as the canal furnace. The furnace had a firebox measuring 75 x 60 x 60 cm. The evolution of this process has reached such a level that today, huge mining, steel, and steel plants with a capacity of several million tons have been created. The iron ore mined is mostly iron oxides, such as magnetite or hematite, which account for 2 to 20 percent of the impurities (such as silicates and aluminates). These impurities are removed from the iron in the furnace and discharged as waste. Refined and concentrated ore enters the furnace in the form of fine powder or fine grains. The most suitable particle size is between 6 and 25 mm. It should be noted that today natural iron sulfide (pyrite) is not used in iron extraction, but its main use is in sulfuric acid. Iron is extracted from its ores during the physical, copper smelting process, and chemical processes under special conditions.
Manufacturing process for iron ore for smelting
In the vicinity of coal, it is regenerated by heat in the furnace and then melted by a stream of hot regenerative gases produced by burning the coke in the hot air below the furnace and moving in the opposite direction of the iron path. The molten iron and pulp from the ore are discharged from the furnace every two to four hours. If the raw material is continuously fed from the top of the furnace, then the furnace can operate continuously. The product of the blast furnace is cast iron, which must be modified to convert it to other iron derivatives, especially steel. In the initial stage, the ore must be condensed in several stages of operation, including crushing, grinding, grinding, washing, using a magnetic separator, or by the flotation method. The concentrated solution usually contains 60 to 65 percent iron, 8 to 12 percent silica. After the ore is concentrated, it should be converted to sizes of 6 to 25 mm, which are suitable for feeding kilns and kilns, which is called agglomeration. Iron is extracted from its quarries mainly by blast furnaces, which is actually a large chemical reactor in which a a mixture of limestone, iron smelting furnace and coal is heated.
You can contact us to buy and sell this product:
Sales consultant: Ms. Leila Nematzadeh
Ways of communication: Phone number: 02147623014
Phone number: 04133660491
Phone number: 09120169267
WhatsApp Response (Skype): click
Instagram: simurgh_steel_company@
email: info@simurghsteelco.com
email: ironore110@gmail.com
Facebook: ironore110@
LinkedIn: simurgh-iron-and-steel-company-a68295180@
twitter: CoSimurgh@