Hot briquetted iron manufacturer
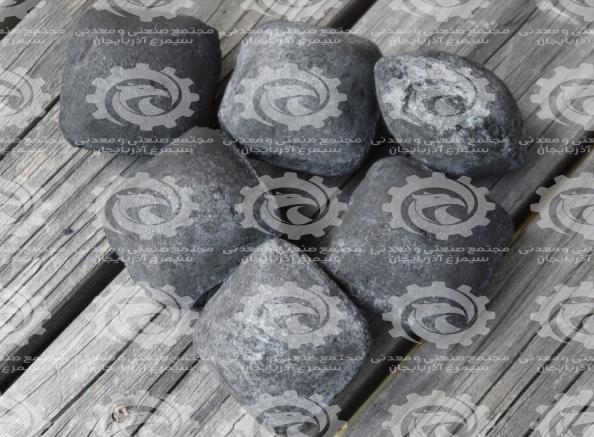
If the sponge iron remains unprotected, it is highly sensitive to oxidation and rusting and must be converted to steel immediately. Iron flakes are likely to burn because they are flammable. Unlike scrap iron, which is almost pure hot briquetted iron, sponge iron has silicon impurities that must be separated during the manufacturing process.
Global analysis of hot briquetted iron
Its production process is at a temperature of more than 650. C. Features of this type of briquette are ease of transportation and its resistance to oxidation, durability, and high mechanical strength. This type of briquette is the most popular product for easy and safe transportation of sponge iron in the world. Due to the limited production volume of sponge iron and its not-so-good properties, it is never marketed as a commercial product. And it is used only for the optimal use of peripheral products of the direct regeneration unit. Cold sponge iron is produced in many direct regeneration units in the world and due to its low resistance to abrasion and poor mechanical properties, the process of transportation and storage is associated with problems and is very expensive. In order to solve this problem and enter the global market, the cold iron and carbon briquettes (CBIC) product will be offered as a new product. CBIC is a product produced in the briquetting process from cold sponge iron. This product has good mechanical strength and chemical resistance and has the ability to be stored and transported in the direct regeneration industry.
Manufacturing process of hot briquetted iron
Sponge iron is one of the direct reduction of iron ore (Direct Reduced Iron). Iron ore means the same pellet that its oxygen is removed during the immediate recovery operation, without the need for iron ore smelting. The appearance of sponge iron in the form of porous spherical parts (pellets) which has a spongy appearance. That’s why it’s called sponge iron. Sponge iron has a high grade of iron, which is more common today due to the lack of iron waste and its increase in price, as well as environmental problems. Sponge iron has a percentage of iron equivalent to scrap iron (between 90 and 94 percent), so fodder is a good material to use in small workshops and allows for higher purity grades using lower purity scrap. Bricked hot iron (HBI) is a compact form of DRI that can be transported, moved, and stored. Iron Direct Iron Reduction (HDRI) Iron does not cool before being discharged from the electric furnace, which is immediately transferred to an electric arc furnace, thus saving energy. The direct reduction process uses direct reduced iron prices or natural ore. An exception is the fluid bed process, which requires a larger size of iron ore particles.The direct reduction process can use natural gas contaminated with neutral gases, and there is no need to remove these gases for other uses. However, any inert gas pollution (metallization of dri) reduces gas flow and thermal efficiency of this process. The sources of powdered iron ore and crude natural gas have both greatly reduced gas transportation costs in areas such as North Australia.
You can contact us to buy and sell this product:
Sales consultant: Ms. Leila Nematzadeh
Ways of communication: Phone number: 02147623014
Phone number: 04133660491
Phone number: 09120169267
WhatsApp Response (Skype): click
Instagram: simurgh_steel_company@
email: info@simurghsteelco.com
email: ironore110@gmail.com
Facebook: ironore110@
LinkedIn: simurgh-iron-and-steel-company-a68295180@
twitter: CoSimurgh@