Direct reduction iron products for sale
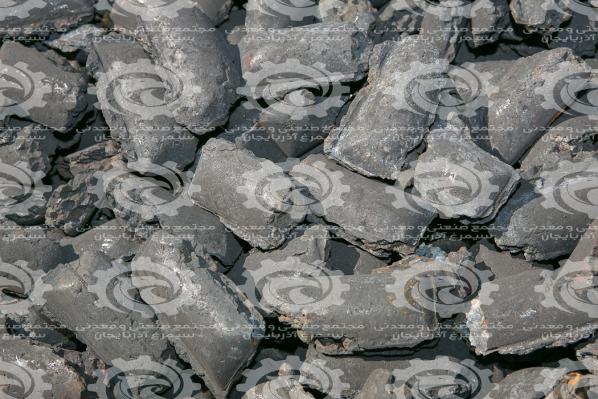
Environmental harms and energy consumption of melt preparation led to the emergence of a new method of iron production called direct reduction iron. In this method, the reduction agent and conversion of iron oxide to metal iron is natural gas and the direct reduction process occurs in the solid state. In this method, the iron ore is pelletized after grinding and enters the reactor. Natural gas also enters the reactor after being broken down and converted to H2 and CO, and the pellet (iron oxide) is converted to sponge iron (metallic iron) after reduction in solid state. In direct reduction, the percentage of metallization (conversion rate of oxide iron to metallic iron) is above 90%, but for use and steelmaking, sponge iron pellets are transferred to an electric arc furnace (EAF) and after removing impurities and reaching the appropriate composition as primary products They are prepared like slabs. For more information about Direct reduction iron products for sale, visit our site.
What is direct reduced iron used for?
Direct reduction of sponge iron has a short history of 50 years compared to the old and traditional method of iron production by blast furnace. The production of iron through blast furnaces has many advantages that no method has yet been able to replace, and 94% of the world’s iron is still produced from that method, but reasons such as environmental issues and declining coal reserves have led to new methods of iron recovery. Direct reduction or production of sponge iron was first performed by American and Mexican researchers in the 1970s.
Resuscitation is performed in direct resuscitation methods, such as in the abdomen of a high furnace, and the resuscitation gas acts on iron oxide and regenerates it in several steps. The iron oxide feed in this method is in the form of porous pellets to be able to pass the reducing gas.
Reduction gas in direct reduction reactors Before entering the reactor, in the reformers, natural gas (CH4) is broken down and converted to CO and H2, and after preheating to a temperature of 1000 ° C, they enter the direct reduction reactor. In direct reduction methods, at least 90% of the iron oxide in the pellet is converted to metallic iron, which is the ratio of the total iron formed to the total iron in the pellet to the percentage of metallization. The product of the direct reduction reactor, which is a solid sponge iron, is easily charged directly to electric arc furnaces (EAF) at a temperature of about 600 ° C and refined and steelmaking is performed on it, reduced iron chemical formula. Most iron ores are mined by surface mining. There are some underground mines, but where possible, surface mining is preferred because it is cheaper. On average, the ore grade is about 60 to 65%, concentrating and increasing the ore grade depending on its initial grade, which includes crushing, milling and physical and magnetic methods.
Purchase direct reduction iron in bulk
The product of these processes, which has a higher percentage of iron than ore, is called concentrate. Crushing and screening are simple mechanical operations that do not change the composition of the rock, but some rocks must be upgraded before melting. Most concentrating processes rely on differences in density to separate light minerals from heavier ones, in some cases to separate crushed iron ore from impurities. For more information about direct reduced iron prices you can visit our site and Purchase direct reduction iron in bulk.
You can contact us to buy and sell this product:
Sales consultant: Ms. Leila Nematzadeh
Ways of communication: Phone number: 02147623014
Phone number: 04133660491
Phone number: 09120169267
WhatsApp Response (Skype): click
Instagram: simurgh_steel_company@
email: info@simurghsteelco.com
email: ironore110@gmail.com
Facebook: ironore110@
LinkedIn: simurgh-iron-and-steel-company-a68295180@
twitter: CoSimurgh@