Direct reduced iron composition Price Fluctuation
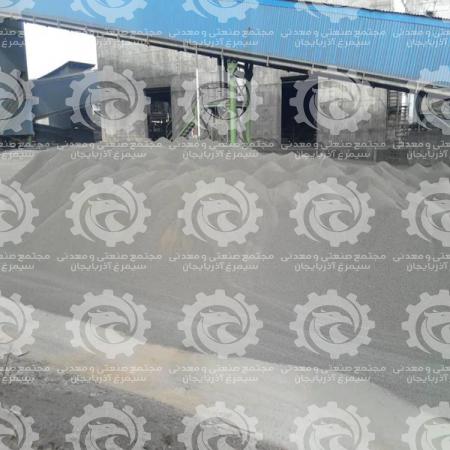
Iron ore obtained from mines is of low grade and must be refined. After extracting iron ore, it is first prepared in several stages for processing and import into the furnace. These steps include crushing, grinding, screening and then washing. Finally, by using the flotation method or using magnetic separators, the grade is increased to about 65-60%. For more information on Direct reduced iron composition Price Fluctuation, visit our site.
Comprehensive Guide for buying direct reduced iron composition
In furnaces called blast furnaces, concentrated iron ore, along with limestone and coke, is exposed to high temperatures. Next, the metal is melted by heat and the flow of coke gases. Molten iron and pulp from its rock impurities are gradually discharged from the furnace. In this system, the furnace is constantly charged with new pieces of metal ore and molten iron is formed from it. The processing product in this furnace is cast iron, which is used in some industries. But most metal structures and metalworking industries require a very durable form called steel. For this reason, cast iron is reprocessed to obtain the required steel. The furnace temperature also reaches 1925 degrees Celsius and the output of the furnace is molten iron with carbon monoxide gases.
The reaction inside these furnaces is also known as direct reduction. It is a reaction in which primary iron ore is reduced by solid or gaseous reducing agents. Finally, the product of this reaction is called cast iron or steel, depending on the percentage of carbon in it. Two common minerals in the composition of iron ore are as hematite and magnetite. This mineral contains about 70% (Fe) and 30% oxygen. This mineral is dyeing and production of anti-corrosion. Another called magnetite is derived from the Greek word meaning magnet. The chemical formula of magnetite mineral is Fe3O4 and contains 72% of Fe.
Of course, there are other types of iron ore that are by the minerals that make them, zeolite, limonite, siderite, grenalite, marcalite, and so on. The first step in obtaining crude sources of iron ore is to identify the ores rich in which is done by engineers and mining professionals. After identifying potential mines, iron ore is mined and to separate impurities and obtain pure metal. Refined iron is obtained as a dark powder that is very to oxidation and impact.
In fact, in order to be suitable for use in strong metal structures in industries such as construction, it must first be combined with other elements. The combination of iron with other elements, usually carbon, nickel, and chromium, is called an alloy. China is the largest importer and consumer of this stone among other countries. Australia and Brazil are also the largest producers in the world. For more information about cold direct reduced iron, visit our site.
Price changes of direct reduced iron composition
To purify this stone, the melting and reduction process must be performed in kilns in the usual way today. This rock is one of the most abundant metal rocks on Earth, so that it can be said that about 5% of the total earth’s crust is iron oxide. For more information about direct reduced iron process and Price changes of direct reduced iron composition, visit our site.
You can contact us to buy and sell this product:
Sales consultant: Ms. Leila Nematzadeh
Ways of communication: Phone number: 02147623014
Phone number: 04133660491
Phone number: 09120169267
WhatsApp Response (Skype): click
Instagram: simurgh_steel_company@
email: info@simurghsteelco.com
email: ironore110@gmail.com
Facebook: ironore110@
LinkedIn: simurgh-iron-and-steel-company-a68295180@
twitter: CoSimurgh@