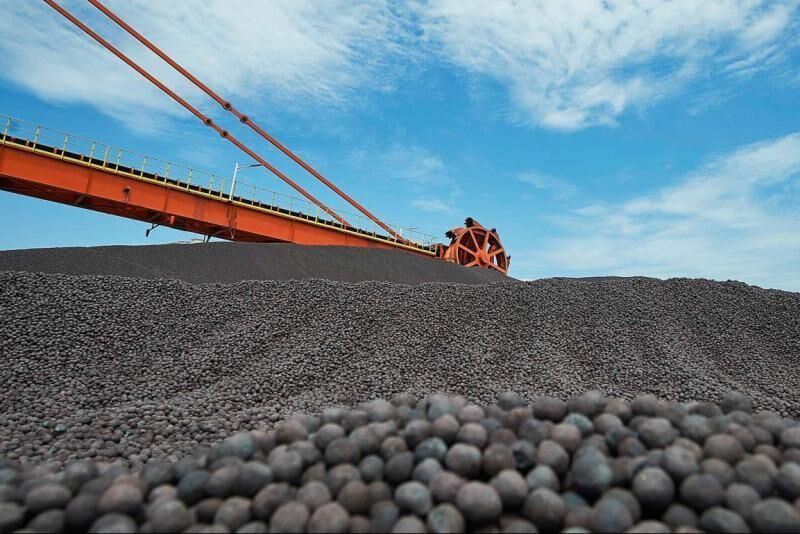
Today, to process and manufacture Steel, we have two methods. Oxygen furnace and electric arc furnace. Finmet process is a process using DRI sludges to produce fine steels. The price of such process is lower than other methods. DRI and HBI, cast Iron and hot metal are the materials produced from Iron ore which we use them during finmet process. The advantage of this process is that Iron Ore could be used directly in the process and there is no need of cooking and using pellet fines. Sludge is another important product used in the steel production process which derives from sponge iron. This product comes in powder form and today its importance shows more than before because of its usage at important industries. Buying this product in bulk is the best and the most cost-effective way. The first development, using the FB and DRI, started in the 1950’s. The FIOR was business established and started by ESSO company in the U.S., which started its work in 1976 in Venezuela and continued its work up until 2000. The FINMET technology is the substitute for FIOR method which was a dual investment between Venezuela and Austria. This development led to establishment of two industrial factory in west Australia and Venezuela with 2 million tons HBI production capacity.
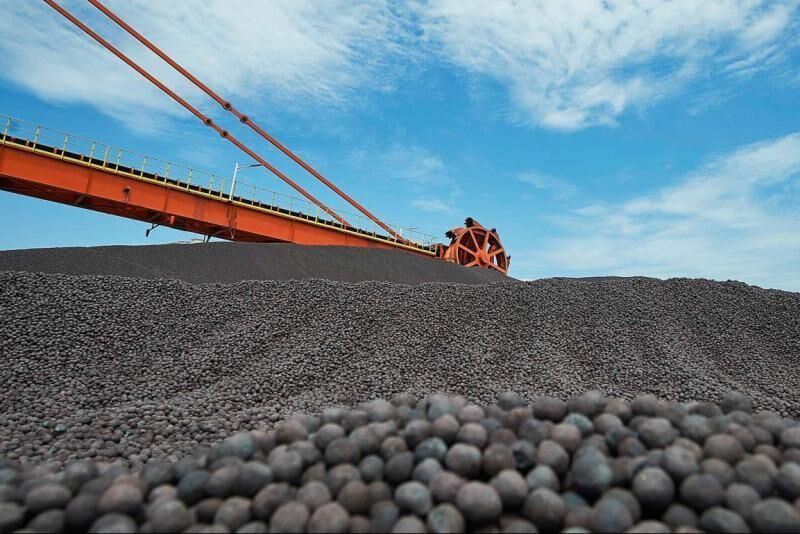
direct reduction iron process
sponge Iron is derived from Direct reduction Iron process, which during this process without melting the Iron Ore we eliminate oxygen. The physical attribute of sponge Iron is circular which the name has came from. The purity of sponge Iron is between 84 to 95 percent. The high rate of purity in sponge iron is a good source to produce steel and iron. The sponge iron is byproduct of natural iron or processed Iron which haven’t got to the melting point. We use the Midrex technology to revive Iron ore. In this technology without a mediator, we revive the Iron pellets. In this method the iron pellet with 67% purity is revived and sponge iron is produced through metallization process. The sponge iron is used as slabs and ingots in steel producing process after melting and reviving process happens. Today about 5% of steel production of the world comes from DRI and the number is growing. The rate of pellet fines used in the process of DRI production is about 45.1 tons for each ton. There are two ways to produce sponge Iron. With natural gas, using coal and Midrex.
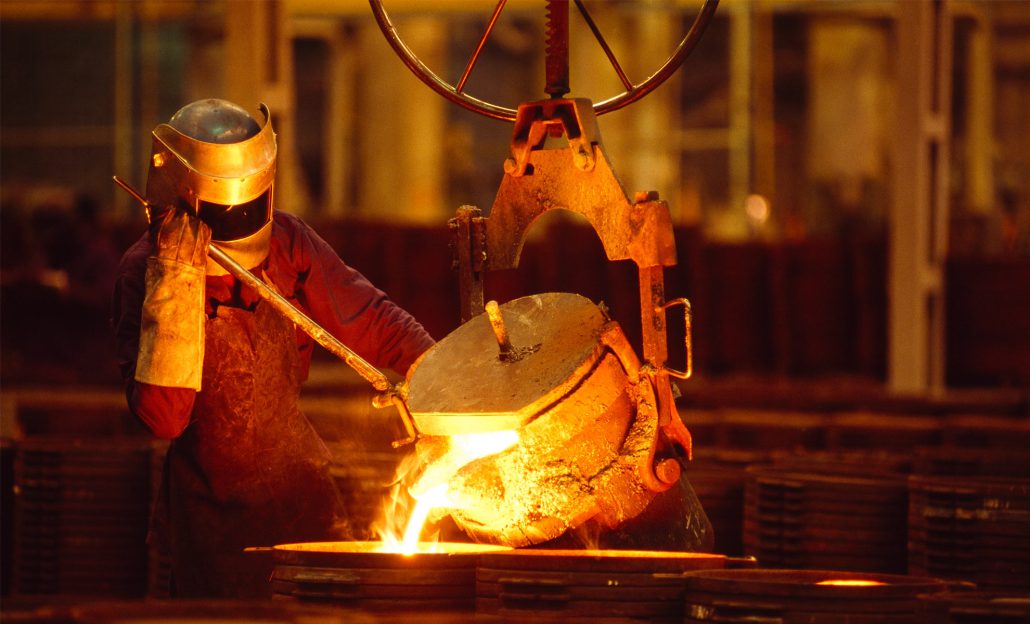
Gas-based DRI process
Gas-based DRI processes are H.Y.L method, Purofer method and Midrex. In the production process of steel and crude Iron we use the conventional methods. In these methods, coke is used as the mediator and heat producer to revive the iron oxides. Converters and coke are not used in the modern technology to produce Iron and other methods like gas based DRI are used. Sponge iron production with DRI process has a good effect on the environment in comparison with other processes. There are some factors directly effecting the process of making sponge Iron. The effects of temperature of reviving speed and side effects. The effects of temperature and the quality of reviving gases entering the reviving reactors. The importance of impurities and their effect on electricity consumption during the steel making and refinement process are the important counter measures in steel production process. There are some stages in steel production line: 1. Condensation, to extract the Iron Ore, surface mining is the first option because it is more economic than other methods. On average the purity of Iron Ore is about 60 to 65 percent, the condensation process and purifying is based on the first percentage of the Iron ore. The product of such process is the purer Iron which is called concentration. 2. Pellet refining, the Iron ore is a powder which is not good to be used in the furnace, so this concentration should be oligomerized in the pellet refining process. There are some other processes which are not very important.
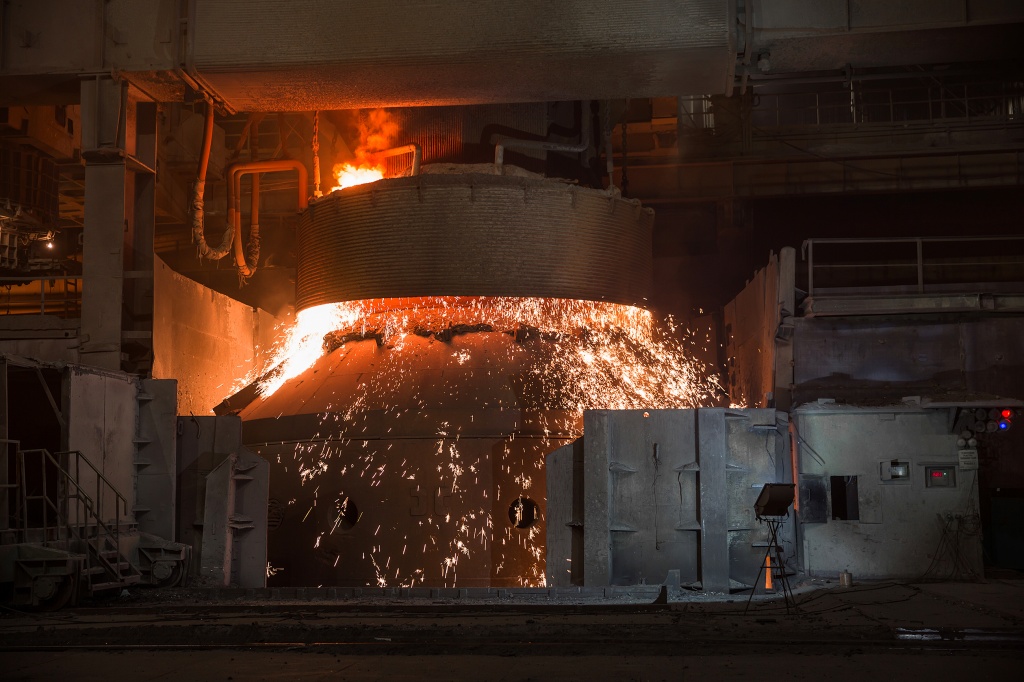
Coal-based DRI process
Using the materials which have less business worth and without using the metallurgic processes lead to less costs on Coal-based DRI process and production. The deleting the costly stage of pellet fining and water usage is another advantage of coal-based processes. With taking aid from X ray and chemical disintegration, the kind and percentage of Iron and steel products are revived to 96 percent and average Iron percentage of the product was about 80 percent during this process. For manufacturing steel, using electric arc furnace is one of the economic and simple ways in comparison with converter tall furnace. Based on the abundancy of coke coal the limitations of using them, they are still the best ways to use.
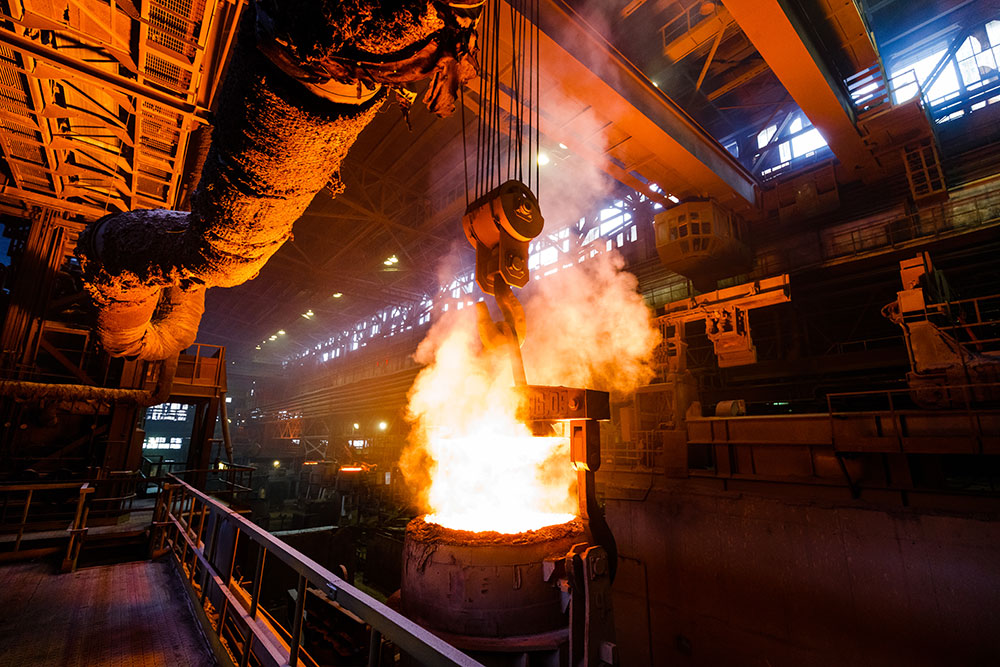
DRI steel hydrogen
Midrex and HYL are the most functional methods to purify and revive DRI steel using Hydrogen. The production of hydrogen in HYL method are based on breaking Methane with water steam in 750 degree silicious and in Midrex method with using water and carbon dioxide going into action with methane in 1177 silicious, leads to better reviving level of Iron and steel. Hydrogen is one of the gases derived from methane and water to break the iron cells and purify the steel and Iron products. The hydrogen can be found in the nature specially in coal which is one of fossil fuels found in the surface of earth and because it is the most frequent element on earth, can easily be mixed with other materials and elements. Eurofer organization is working so hard to make a synced net to manufacture and produce hydrogen to industries especially steel industry.
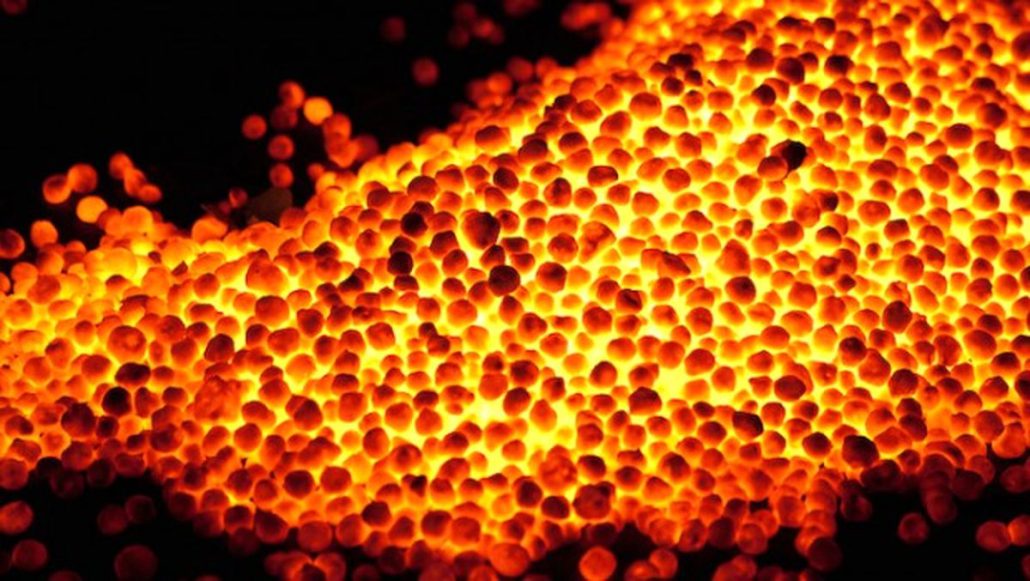
DRI vs blast furnace
There are some huge differences between DRI and blast furnaces which show that DRI furnace and method are the best now to get the best quality products possible. In this factory and company, we are working the best ways possible to get to the best quality product. As mentioned above DRI are the first stage of refining and reviving the iron and steel, and in our factories, we are using the same methods to give you the best product possible. Every quality and quantity possible in the market is possible to purchase through our website. Trust us. We always put our costumers first.
You can contact us to buy and sell this product:
Sales consultant: Ms. Leila Nematzadeh
Ways of communication: Phone number: 02147623014
Phone number: 04133660491
Phone number: 09120169267
WhatsApp Response (Skype): click
Instagram: simurgh_steel_company@
email: info@simurghsteelco.com
email: ironore110@gmail.com
Facebook: ironore110@
LinkedIn: simurgh-iron-and-steel-company-a68295180@
twitter: CoSimurgh@